Engineering Insights
Heating Elements
THIS ARTICLE IDENTIFIES DIFFERENT TYPES OF ELECTRIC HEATING ELEMENTS, HIGHLIGHTS IMPORTANT CONSIDERATIONS WHEN DETERMINING A HEATER SOLUTION, AND FINALLY LOOKS AT SOME OF THE LESS OBVIOUS COSTS. EXAMPLES FROM EXPERIENCE AS WELL AS IN-HOUSE ENGINEERING WHITE PAPERS ARE REFERENCED THROUGHOUT THE ARTICLE.
Heating ElementsWhat is a Heating Element? A heating element is a component composed of both electrically conductive as well as insulating material, designed to serve a heating purpose. Let’s break that down. Component: A heating element is more than the heating alloy alone. It is an assemblage of parts that includes a framework of insulating material as well as lead connectors. In the case of an open coil heater, for example, the heating alloy is typically held or suspended by mica or ceramic insulators. Wire terminals safely connect the heater coils to the circuit. Electrically Conductive: The fundamental core of an electric heater is the heating element alloy within that turns electrical energy into heat energy when subjected to a current. It is the part of a heater where the electrical load occurs. When heat is produced in this way we call it Resistive Heating. It is also known as Joule Heating. Designed to Serve a Purpose: A heating element is more than its material makeup. It is a product of design. Alloy and insulators must be manipulated to become a useful component that serves a heating purpose. The multi-talented craftsman who determines the alloy and gives the heater it forms is the heater design engineer.
Types and Material
The material at the heart of a heater is commonly metal in the shape of a wire, ribbon or a design etched from a metal foil. A heater may also contain ceramic, plastic, or silicone impregnated with a conductor. Choosing the best materials for the job includes a thorough understanding of material properties as well as knowing where to source the best supplies for the particular application.
Metal Wire and Ribbon Alloys
All metal heating elements have physical, thermal, electrical, and metallurgical properties. These material properties are necessary considerations when choosing the best solution for an application. Temperature-dependent differences such as electrical resistance and thermal expansion will vary depending upon the material. Many heater design challenges arise as the properties of various heating element materials tend to change based on conditions.
Heating elements found in common appliances are made from metallic resistance alloys such as Fe-Cr-Al and Ni-Cr(Fe). They have the ability to produce temperatures hot enough to get the element to glow red hot, in the neighborhood of 1112°F (600°C) and above. Heaters that operate below this range can be made from a much wider range of materials. Elements such as Copper, Nickel, Aluminum, Molybdenum, Iron, and Tungsten as well as alloys containing combinations of these elements are used.
Resistance heating alloys contain varying proportions of chemical elements depending upon the wire you order and who makes it. A Nickel base alloy we commonly use is 80 Ni, 20 Cr (80% Nickel, 20% Chromium). The proportions of its composition are different from those of 60 Ni, 16 Cr (60% Nickel, 16% Chromium), The different properties these two alloys exhibit are significant. A clever engineer capitalizes on material properties to achieve better efficiency, reliability, performance, cost, and safety in your application.
Wire Elements within a Framework
Electrically conductive heating element wire exists within a framework of electrically insulating material. Whether corrugated, coiled or straight, wire elements typically fall into one of three classifications depending on how they physically make contact with their surrounding framework. Those distinctions are referred to as either suspended, embedded, or supported. They affect how the heater is made and how heat can be transferred.
Suspended
Ceramic or mica is typically used to suspend the wire at two or more points. The number of points involves tradeoffs. On one hand, we may seek to limit the number of contact points to reduce complexity, material, and manufacturing costs. On the other hand, we may seek to add points of contact to support an airflow and minimize element sag. Suspended elements transfer heat by convection and radiation. Not conduction.
Embedded
In an embedded heating element, the wire is encased in an insulating material. Since it is in complete contact with its surroundings, the element can only transfer heat by way of conduction. An example of this is a cartridge heater. The heating element coil is locked inside of an insulating MgO material. The heat transfers directly from the wire coil to the MgO and on to the outer sheath that heats the platen.
Supported
This type of integration with a heater framework falls somewhere between suspended and embedded. A large amount of the heating element will be well supported at many contact points. It may in fact be a coil laying in a channel. It is not embedded in insulation material and as such the coil will have some freedom in movement. Conduction, convection, and radiation are all forms of heat transfer from a Supported element.
Trace Elements
A specific resistance alloy from one heating element manufacturer will not necessarily exhibit the same properties when supplied by a different manufacturer. These seemingly similar products may have trace elements in addition to their namesake elements, which can drastically affect alloy properties.
Trace elements come in two varieties, contaminates and enhancements. Contaminates have an undesirable effect such as shorter life and limited temperature range. Trace element enhancements are added on purpose by the manufacturer. Improvements include increased oxide layer adhesion, greater ability to hold a shape, and longer wire life at higher temperatures.
An experienced design engineer will compare alloy properties, filter through tradeoffs, and arrive at the best heating element alloy and material dimensions for the job. He will then work with production to manipulate the material into a dimensional shape and orientation that produces the best outcome for your application. A good custom heater shop is going to understand how wire and ribbon alloy producers stack up. They have their eye on the market, good vendor relationships, and favorably negotiated material prices.
Process Air Heaters
Process Air Heaters are hot air components used in industrial and commercial processes. Each one is designed to work within a range of temperatures, airflows, and air pressures. Applications include drying, curing, melting, cutting, baking, heat shrinking, de-soldering, metallization, heat staking, sterilization, air scrubbing, laminating, adhesive activation, hot air curtains, and air knives.
A power flow rate temperature calculator uses a formula like Watts = SCFM x ΔT/3 to quickly determine the minimum required wattage for an application. Our visual version of this calculator helps to make the relationship among these variables more intuitive.
Open Coil Open coil heaters employ electrically conductive coils commonly made from NiCr or FeCrAl and held or suspended by insulators such as ceramic or mica. They are designed to expose the heating element surface area directly to an airflow. The coil shape allows the designer to pack in a greater amount of heated surface area, increasing contact with the air.
Minimal blockage of the air (resulting in a lower air pressure drop), uniform element temperature, and reduced areas of element contact without sag are concerns of the heater design engineer. The choice of alloy, gauge, and dimensions are strategically chosen to create a custom solution based on an application’s unique needs. When conditions are predominantly convective the temperature of a helical shaped wire can be estimated in an iterative process with a spreadsheet. Click here to read Dexter Diepholz’s approach.
Serpentine™ Serpentine Technology™ dates back to TUTCO-SureHeat origins when GTE Sylvania patented the first design. It has since been the basis for many TUTCO SureHeat high-temperature products.
Serpentine™ is used in demanding Process Air Heater applications. Heaters that employ Serpentine Technology™ contain wire elements wrapped in a protruding fashion around a non-electrically conducting core. Unlike coils that would otherwise follow a uniform loop pattern down the length of a tube, Serpentine Technology™ introduces each loop or coil to an airflow apart from its neighboring loops.
Also, unlike open coils that need to be suspended, Serpentine Technology™ is somewhat stiff so the elements can hold their shape around an insulating core. Serpentine Technology™ uses low mass high watt density material and must be controlled carefully to avoid damage that occurs from the elements getting too hot or ramping too quickly without adequate airflow. A closed-loop set-up with a fast control loop (200ms or better) is critical to avoid overshoot in high-temperature applications.
Serpentine™ can be assembled in a single process air heater to produce exceptional amounts of heat energy. These heaters are often custom manufactured and referred to as Specialty Flanged Inline heaters or SFI for short. SFI heaters can be mammoth in size. In some cases, entire power facilities are built to support the electricity required to operate them. SFI is popular in the areas of combustion research, supersonic and hypersonic wind tunnel, maintenance repair and overhaul (MRO) testing, military applications, and university research. SFI heaters are replacing gas heaters in applications where the byproducts of combustion are not desirable.
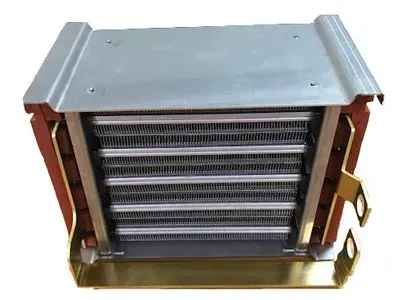
A PTC air heater designed for aircraft environmental control. It contains several PTC heating elements in one package. Temperature limiting means it can never get too hot.
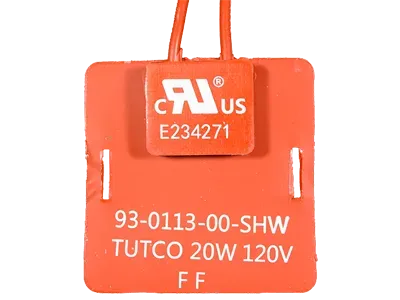
A PTC heater piggybacks this silicone rubber heater acting as a small temperature limiter without the need for bulkier control options. The small evaporator heater design saves the client cost and valuable space within their enclosure.
Flexible Heaters
Flexible heaters (also known as flex heaters) are surface heaters that can be bent to conform to the surface being heated. They can be shaped during manufacturing to fit complex geometries. Flexible heaters contain thin film, foil, or wire wound heating elements manufactured from a wide variety of alloys. They have good dialectic strength and are resistant to many chemicals.
The electrically conductive traces are either attached to a substrate or embedded (sandwiched) inside of multiple layers. They are either cut or etched by way of a chemical process to create the shape of the heating element traces. A wide variety of electrical conductors including stainless, copper, aluminum, nichrome, and more can be used. The choice of which conductor to use will primarily depend upon the desired operating temperature and product cost. Budgetary considerations may include the cost to manufacture, the cost to assemble (how do the lead wires get attached for example), and the cost of the heating element material itself.
Silicone Rubber Heaters
Silicone rubber heaters contain one or more heating elements sandwiched within two pieces of vulcanized silicone rubber. The rubber is electrically insulating yet thermally conductive. The elements within are thin foil alloys that have been etched. They can also be made with wire though this is increasingly less common. Silicone rubber heaters are durable and versatile products offering up to 30 watts per square inch with temperatures up to 220°C (428°F) per UL requirements. They can be designed to be cut into any shape. Their ability to flex makes them suitable for many applications with curved and odd-shaped surfaces. You can learn more about manufacturing silicone rubber heaters in our Engineer Talk white paper.
Polyimide Heaters Also called Kapton, polyimide heaters are similar to silicone rubber heaters in that they are thin flat etched heating elements. They are lighter in weight than silicone and bend more easily. Notable is the very good tensile strength of the substrate (polyimide) material. While their max temperature limit tends to be a bit lower than silicone rubber they have the ability to dial in very precise temperatures and can do so rapidly. Their ultra-thin profile is appealing for applications in electronics, optics, laboratory, medical, aerospace, and anywhere things need to be very small and lightweight. Applications that require the heating of a lens or glass window will sometimes use a transparent material for the dielectric.
Thick Film Heaters
These low-profile (thin) heaters are manufactured with precision equipment to produce two-dimensional geometries in a wide variety of wattages and voltages. Ideally suited for applications that require rapid response and temperature uniformity. The thin profile is well suited where space is limited. These heaters can achieve very high temperatures.
Thick film heaters are manufactured using a silkscreen type process. This allows for different compositions of conductive inks to control the placement of heat. It also allows for flexible shapes. Features include being adaptable to various shapes, uniform conductivity, customize areas of heat concentration, resistance to corrosive environments, a thin profile, and flexible.
PTC Heaters
PTC Heaters (Positive Temperature Coefficient Heaters) contain trace amounts of an electrically conductive material such as carbon black mixed with an electrically insulating yet thermally conductive material such as silicone rubber. Two leads buried within this material do not physically touch. The ratio of electrically conductive vs electrically insulating material is carefully controlled during manufacturing. The most notable property of PTC heating elements is that they increase in electrical resistance as they get hotter. Engineers make good use of this property by designing PTC heaters to cap-out at a specific temperature and thus become self-limiting.
Embedded Elements
The electrically conductive heat generating material is embedded within an electrical insulating yet thermally conductive material.
Cartridge Heaters A cartridge heater contains an electric coil surrounded by an insulating powder (typically magnesium oxide) and packed within a tapered sheath. All terminals exit the same end. This type of heater is commonly inserted into a cylindrical hole. The size and shape of the bore as well as the size and shape of the heating element is extremely important. There should be a firm uniform fit when energized to achieve safe and efficient conductive heat transfer. Not too tight or the heater may need to be drilled out when it expires. In some cases, a cartridge heater is used to heat a fluid instead of a block of metal and will have fins to increase surface area.
Strip Heaters A strip heater is a relatively flat rectangular heater made from a strip of mica that has been wrapped with ribbon wire. That assembly is sandwiched between two more pieces of mica and then encased in a metal sheath. Strip heaters can be outfitted with fins and they can also be specially manufactured for extreme environments. Many terminal styles exist for this heater. Cut-outs and other shape modifications are possible.
Band Heaters If you bend a strip heater into the shape of a ring then you have a band heater. They are clamped around pipes, barrels, and the base of kettles. They are used to heat fluids and to assist in the melting of solids. The later is very common in the plastics processing industry where plastic pellets must be warmed to a sufficient temperature. This does not in itself melt the plastic but prepares the material for the mechanical process that actually does the melting. Sufficient heat is required for the retraction of a large auger used in many plastic manufacturing processes.
Tubular Heaters Tubular heaters have an electric coil surrounded by a ceramic insulating powder encased within a metal sheath. The terminals exit opposite ends of the heater. This type of heater typically has a round cross-section though it can be manufactured into other shapes like square or triangular. They are often manufactured with curves and bends to best support an application. A common location to find a tubular element is inside an electric kitchen oven.
Determining a Solution
In order to arrive at a heating solution ideally suited for your particular application, it is useful to understand how a heater will fit into and support a larger system. When engaged in design discussions with a client we ask questions in order to understand the application and to build tenable requirements from which we make design decisions. Initially, we’ll want to know some of the more fundamental requirements.
- What are we heating?
- A fluid? A solid?
- What is the max operating temperature? What is the available power?
Essentially were defining the problem we intend to solve with the heater. Every project is different and has its own unique heating needs. Decisions regarding dimensions, choice of alloy, and overall heater design will be based on your unique project requirements. There may be any number of hidden requirements that will affect the direction of design so we want to dig deeper whenever possible.
We want to know the start and finishing temperatures, flow rates, cycling frequency, ramp speed, peak temperature, electrical power, thermal controls, and physical space. Each project will have its own unique application circumstances such as environmental contaminants, tolerances, safety, factory assembly and budget to name a few. When faced with a thorough list of well thought out requirements, proper design choices can progress.
Power & Temperature
The application will need to supply enough power to run the heater. We're going to want to know the available power and any limitations.
We want to know the minimum amount of power necessary for the application to function properly. A heater does not require the same power all of the time. There are moments in time when a heater will require more power than others. We want to know the most power that will ever be demanded of that heater. In some applications, max power happens when the heater is fired up and making its way to temperature. In other applications peak is demanded while maintaining an operating temperature. Whichever one of these is higher is a minimum power requirement.
We want to know how much power is needed to successfully heat the thing we are heating within the required amount of time. We could be heating a block of steel, a box of air, a tank of oil, or water flowing in a pipe. Each of these scenarios is simple to estimate if you are willing to forgo some precision. You can see calculations with examples in Ian Renwick’s Engineer Talk article, How Much Wattage do I Need? Jerry Sain addresses this specifically for heater coils in his paper, Heater Coil Design.
Our heater design will not only need to safely and reliably handle the power required but it also needs to deliver the heat. We can narrow down our material and dimension choices for many heater shapes with textbook heat transfer calculations. An approach for estimating the temperature produced by a spiral wound wire coil in a flow of gas may be less obvious. Dexter Diepholz outlines an approach for this in his Engineer Talk paper, Estimating the Resistance Wire Temperature for an Open Coil Heating Element.
Watt Density is another useful way to quickly compare materials. Measured in Watts/in2 or Watts/mm2 watt density is the total watts of the heating element divided by the surface area that generates the heat. You can learn more in Dexter's white paper, Why Does Watt Density Always Come Up When Discussion Heating Elements?
Heating Elements and their Environment
Different materials will react differently depending upon their environment. It is useful to know if there will be a high concentration of a particular gas, significant humidity or alloy harming contaminates in the space where the heating element is being energized.
Ammonia, sulfur, zinc, chlorine, and boron will bring an early end to a heater with a poorly matched alloy. For example, chloride contaminates are generally bad for Iron base alloys while sulfides are harmful to Ni-Cr. Process air, industrial cleaners, municipal water supply, and even oil from an installer's fingers may be a source of alloy eating contaminates. You can learn more about extending heater life in Patrick Laws Engineering Talk article, Watts Killing your Heater.
Designing for Preexisting Equipment
It is common for us to design a heater for equipment that has already been designed or even manufactured. It is also a more limiting option. Any opportunity to be involved early in the product design process is going to result in a better product with a better heating solution at a reduced cost.
The amount of allowable space for the heater as well as the shape of the space is often the culprit. If your product requires an open coil heater yet we can’t get proper airflow across the heater coils then that is going to be a problem. Not only does a preexisting product limit your heater design options it can become cost-prohibitive or even impossibly difficult to engineer. We have produced thousands of designs and as such we can spot many of the classic pitfalls before they happen.
While early involvement is ideal, we also recognize that such a luxury is not always possible and we are very happy to work with you to engineer a solution at any stage of your design process. Designing innovative heaters to fit difficult requirements is something we have become quite good at doing. The following are projects that showcase our engineering prowess when faced with pre-existing limitations.
Evaporator Heater
The project required a submersible heater with temperature regulation to fit a very tiny space.
Miniature Heat Torch For Blood Analyzer
Precision field-replaceable air heater with 1″ profile to heat a flow of .4 lmp to 380°F (193.3°C) within 3.5 seconds.
Patient Warming Blanket Heater
Tight space, controlled ramp-up, and safety were the primary concerns for this surgical room product.
Custom Heating Element for Medical Storage Device
This retrofit heater merged the mounting brackets for the fan into the heating element housing.
Internal Heating System for Medical Imaging
Turnkey solution including element, blower, sensor, and controller offers even regulated temperature inside the awkward shape of a CT scanner.
Custom Heating Elements
An off-the-shelf solution is often the first consideration as it will be the easiest short-term path if something suitable exists. This does not mean it will be the best long term value. Product performance, durability, and efficiency are costs not necessarily obvious at the time of purchase.
For products with complex requirements, it may be difficult to find an existing heater that makes the grade. A new piece of lab equipment requiring a fast and controlled ramp-up, a high cycling frequency, and an unusually shaped space is probably going to benefit from a custom heating element solution. In the hands of experience, you have the best opportunity to improve product performance, increase reliability, and reduce cost. You can see examples of custom heating elements on our custom heaters page. Take notice of what a wide variety of shapes and styles result from the needs of a custom application.
Heater Life
Good choices in design and material will improve heater life while poor material-to-application matches and other bad design choices can result in costly field replacements, product damage, safety issues, and unhappy customers.
All resistance heating elements eventually burn out. Oxidation, changes in electrical resistance, damage, and deformation are all factors that limit longevity. An experienced heater design engineer can help you avoid classic mistakes and achieve long heater life for your particular application.
Resistance heating alloys form an oxidation layer at higher temperatures. The layer grows quickly at first as the alloy is easily able to interact with oxygen in the air. As the layer grows it becomes a protective layer inhibiting access to oxygen until eventually preventing further oxidation.
The amount that the heating alloy expands when heated (referred to as an alloy’s coefficient of thermal expansion) is going to be different than that of the oxide layer. That difference in thermal expansion as well as the strength of adhesion (the oxide layer’s adhesion to the alloy) has a strong correlation with heating element longevity.
An oxide layer that remains strongly adhered to the alloy without cracking and spawling will continue to protect the alloy. A heating element with a high coefficient of thermal expansion and poor oxide layer adhesion will not last long in an application with rapid temperature cycling.
Installation & Assembly
The ease in which a heating element integrates with an application affects cost. Difficult and time-consuming product assemblies will burden a manufacturer with labor, unnecessary part inventories, and fewer units going out the door. Field installations and replacements will take longer and may require higher-skilled workers. A heating element designed for a particular product should result in superior integration with that product. This will yield better performance as well as faster field installation and product assembly. In some cases, additional part costs may be removed too. The following are specific examples where we saved the client cost and hassle with install and assembly.
The Cost of Quality
We had a customer in the plastic process industry that had left us because of pricing. They were happy with our quality and our delivery but they wanted a price that we couldn’t meet and still be profitable. Five years pass and we get a phone call. Heaters are failing in the field and they are tired of the poor quality they are getting from their current supplier.
Consider what this is costing them. One of their units requires ten heaters. They get installed and tested. Three fail. Those get yanked out. Then the company has to have its customer service people request an RMF and send it back. When the replacements come back they have to reinstall them and test again. Now they’re late on their units. In addition, they had products failing in the field. It is failing for their customers and they’re paying a field technician to go out and fix their units.
This company started realizing those costs and that is why they came back to us. We modified the heater to perfectly meet their needs. We cost more than the cheaper option upfront but when they realized everything involved they realized that the TUTCO-Farnam solution is a massive cost saving and we’re also saving their reputation.
Conversations Lead to Understanding
The conversation between a specialist and a client is where the real value begins. It takes a willingness to listen and engage. It’s also your best chance to discover any pitfalls and hidden gems. At TUTCO-Farnam we are both application and customer committed. An engineer looks at every opportunity that comes in. We listen and we apply what we’ve learned. Customers often see something on our website and say, ‘hey, that looks like what I want.’ We then work with them to understand the requirements and guide them towards something that is going to work best.
The following are examples where conversations lead to understanding, which subsequently resulted in marked improvements for our clients.
Getting Started with TUTCO Farnam
TUTCO Farnam is a heating element manufacturer specializing in custom heaters large and small. We have used a variety of electrically resistive metal and intermetallic alloys in over 2,000 custom designs. You can find examples of our heating elements on our custom heaters page. Contact us about your unique application needs and see what TUTCO-Farnam can do for you.